FSID
Unlocking Procurement Potential: Reducing Cost & Accelerating Sustainability
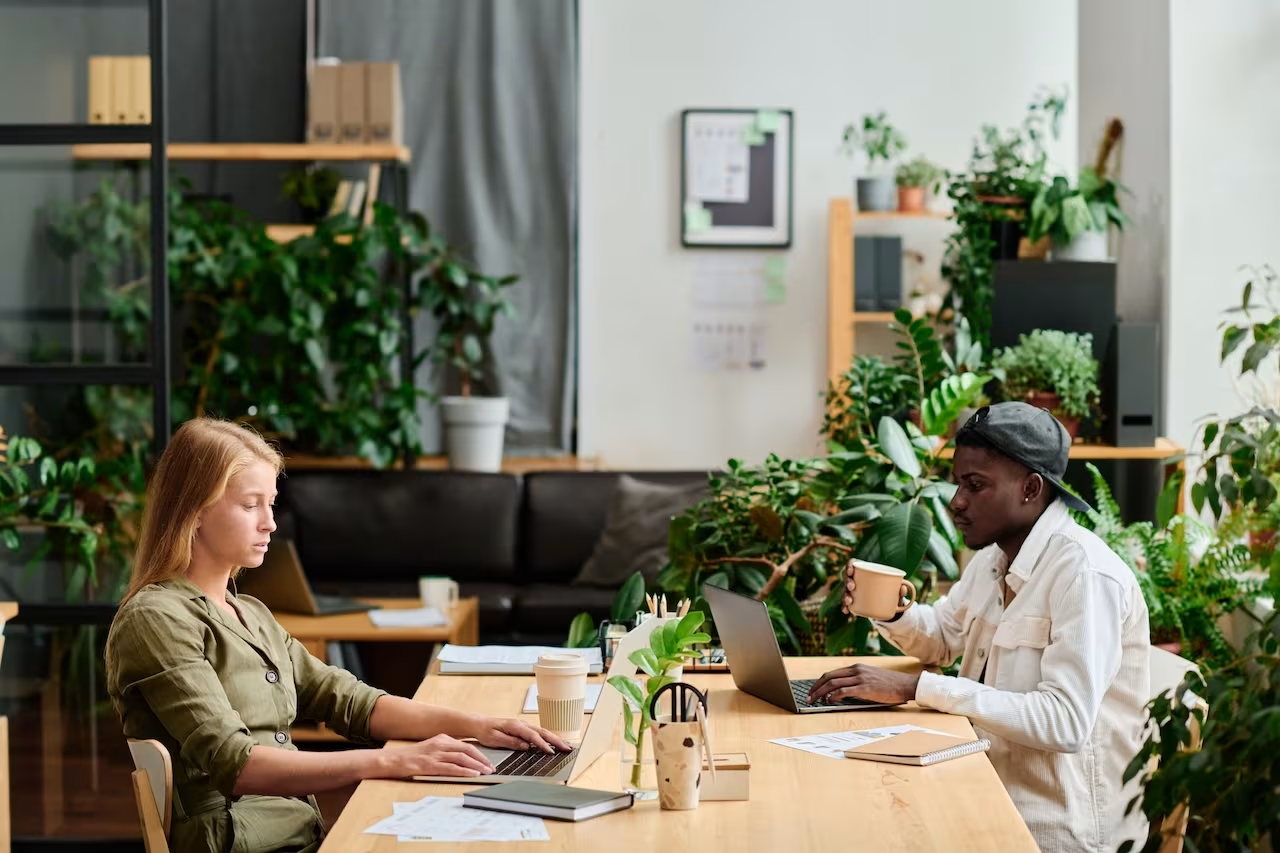
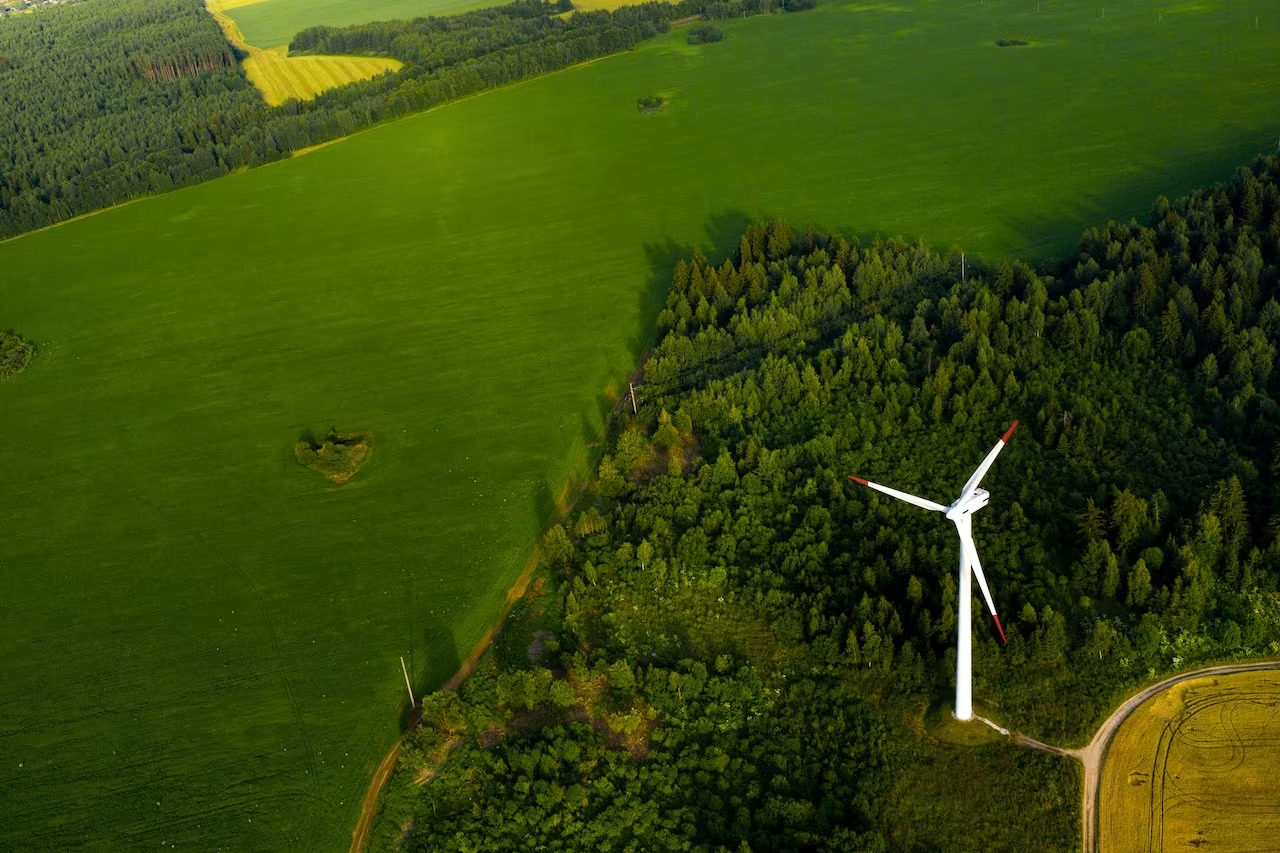
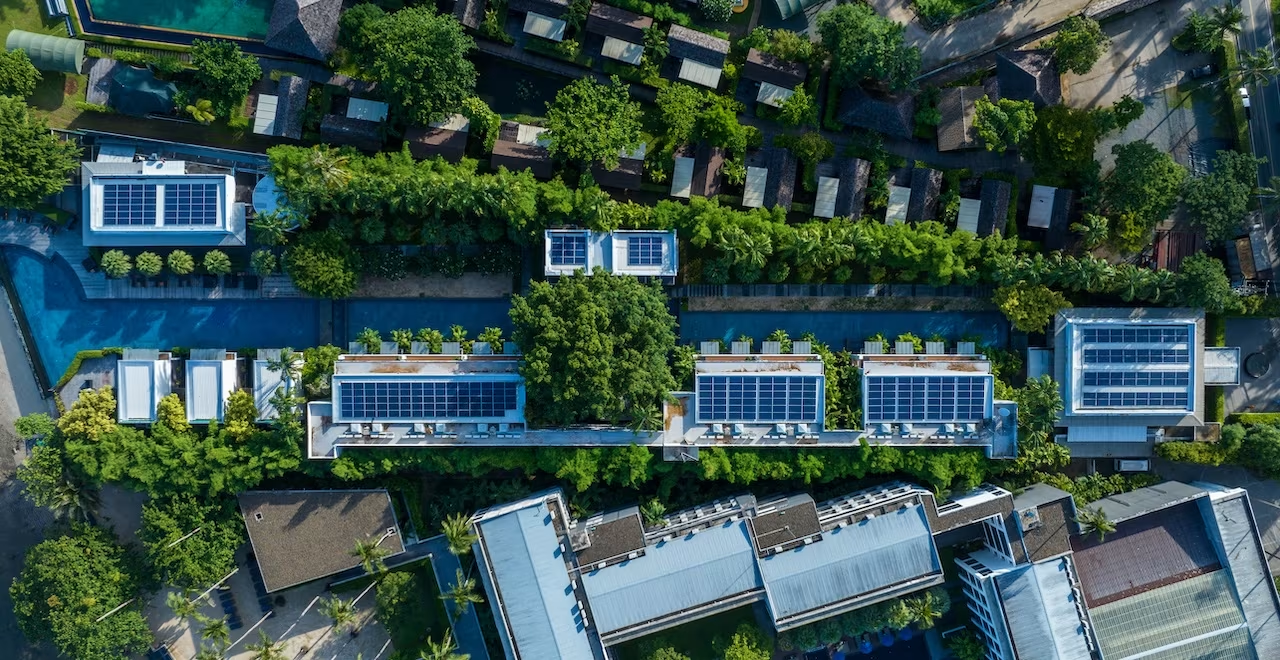
Procurement can control 70% of a company's total costs, making it one of the most important drivers of business performance, innovation, and competitive advantage.
Our mission is to deliver lasting impact, combining seasoned expertise with a proprietary database of sustainable products.
We partner with clients to unlock savings, improve supply chain performance, and meet ambitious ESG goals.
Transforming procurement into a driver of value, resilience, and sustainability. Empowering smarter decisions.
Services
From strategy to execution, we deliver measurable outcomes
Our Process
Discovery, Audit, Diagnostic & Assessment
We provide a clear view of your sustainability opportunities, compliance risks, and procurement performance. We deliver actionable insights, benchmark your position against industry peers, and estimate potential financial and environmental gains — all backed by stakeholder and customer input. You'll also receive clear recommendations for next steps and pricing for future phases.
Cost Optimisation & Sustainability Strategy
We building a clear and ambitious plan to accelerate progress toward your vision. We define measurable targets and benchmarks to track success, create a detailed roadmap and work plan for implementation, and establish a governance framework to ensure a smooth transition into execution.
Implementation and Management
We target quick wins by identifying and executing “low-hanging fruit” opportunities for immediate impact. We pilot and scale cost reduction and sustainability initiatives, working closely with key stakeholders and suppliers to foster collaboration. Procurement processes are redesigned to embed sustainability into everyday operations, and integrated technology solutions are deployed to streamline data management and decision-making.
Ongoing Support and Reporting
We provide tooling solutions to embed best practices across your organization and deliver ongoing support to maintain momentum and continuously improve procurement processes. Our team facilitates supplier collaboration initiatives to drive shared value and offers expert consulting on sustainable product design, helping extend sustainability impact across your entire offering.
- 1
- 2
- 3
- 4